Common mistakes in load restraint include: underestimating the importance of friction, incorrect use of tie-down lashings, the failure to stabilise tall loads, neglecing regular checks and using damaged or inadequate equipment. Unfortunately, even experienced transport operators can make mistakes that compromise the security of their loads, endanger road users, and result in costly damages. Here, we highlight some of the most common mistakes in load restraint and offer practical advice on how to avoid them.
1. Underestimating the Importance of Friction
One of the most common errors is overlooking the role of friction in load restraint. Relying solely on the weight of the load to keep it in place is a dangerous misconception. The NHVR Load Restraint Guide emphasises that friction alone is often insufficient to prevent movement, especially on smooth surfaces like steel decks. To enhance friction, operators should use anti-slip mats or other friction-enhancing materials between the load and the vehicle deck (Load Restraint Guide).
Tip: Always assess the friction level between your load and the deck. If necessary, increase friction with appropriate materials and use adequate tie-downs to ensure the load remains stable.
2. Incorrect Use of Tie-Down Lashings
Tie-down lashings are crucial for securing loads, but they are often misused. Common mistakes include incorrect lashing angles, inadequate tension, and insufficient lashings. The effectiveness of tie-downs decreases as the lashing angle becomes more horizontal (see table 1), requiring more lashings to achieve the same clamping force.
Tip: Ensure your lashings are as vertical as possible. Use the tie-down checklist provided in the Load Restraint Guide to verify that your lashings are correctly tensioned and positioned.
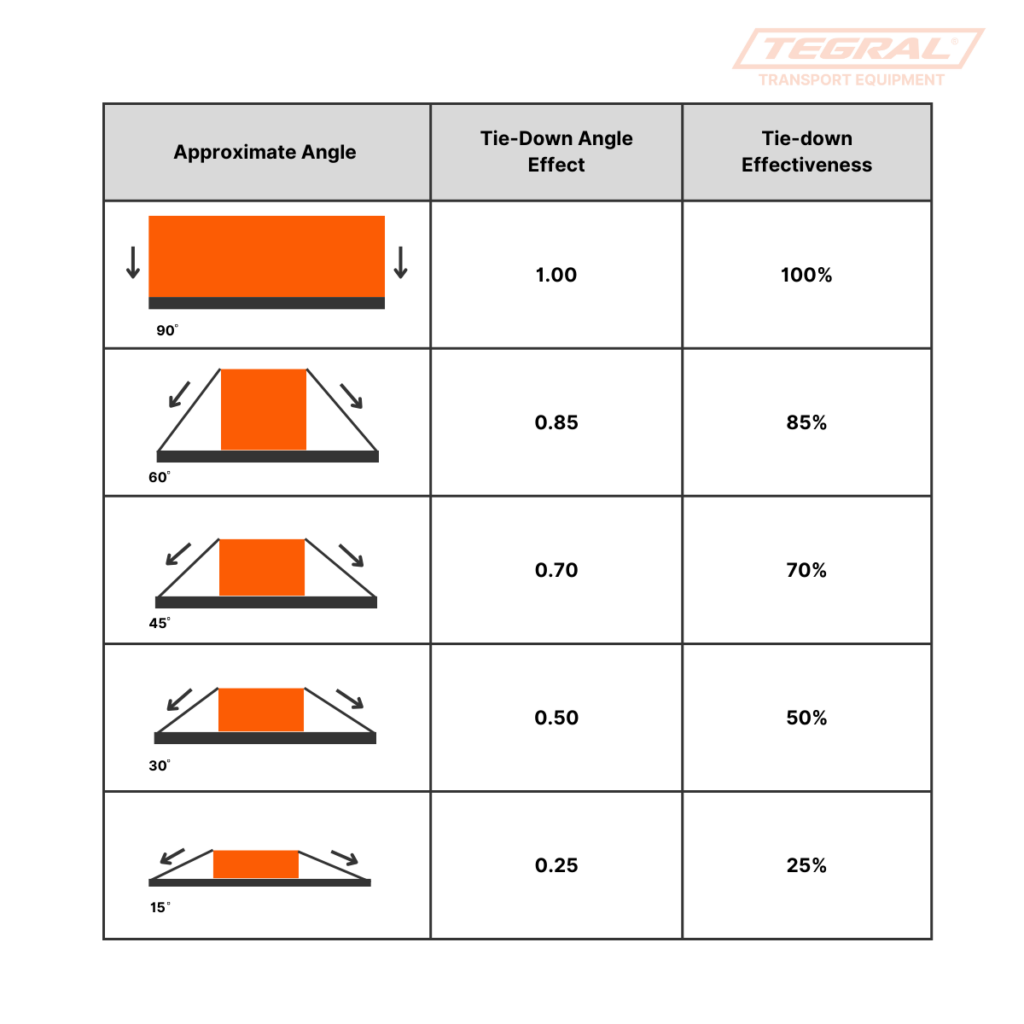
3. Failure to Stabilise Tall Loads
Tall loads are particularly prone to tipping, especially during sudden stops or sharp turns. A load that is unstable at the base is likely to topple even if it is restrained correctly at the bottom. The Load Restraint Guide advises placing tall, unstable loads against a rigid structure or using additional lashings to prevent tipping.
Tip: Always assess the stability of tall loads. Use chocks, cradles, or headboards to secure the base and prevent the load from tipping during transit.
4. Neglecting Regular Checks During Transit
Loads can shift during a journey, leading to loosened restraints and increased risk of movement. One of the key recommendations from the Load Restraint Guide is to regularly check your load and its restraints during transit, particularly after driving on rough roads or making sharp turns.
Tip: Plan regular stops to inspect and re-tighten lashings as needed, especially after driving on uneven terrain. This simple practice can prevent accidents and ensure the safety of your cargo.
5. Using Damaged or Inadequate Restraint Equipment
Worn or damaged restraint equipment significantly reduces its effectiveness, yet it is a common mistake to use it in the hope that it will hold up. The Load Restraint Guide stresses the importance of inspecting all equipment before each trip and replacing any that show signs of wear or damage. For example, if a piece of webbing is weakened by 10% or more, you should replace you strap.
Tip: Develop a routine inspection process for all load restraint equipment. Replace any components that do not meet the required safety standards to ensure your load is securely restrained.
For more detailed guidance, refer to the Load Restraint Guide, which provides comprehensive information on the correct methods and equipment to use for various load types.
You may Also Be Interested In
Australian Freight Industry Overview
Gympie Bypass Set to Open in October, Marking End of 15-Year Highway Upgrade
Load Restraint Best Practices: Industry-Specific Tips for Safety and Compliance